Craftmanship
Craftsmen
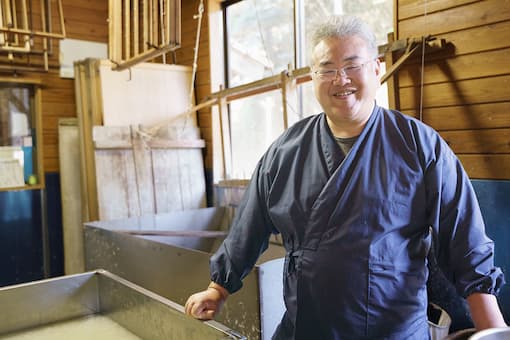
Washi Paper Craftsman
Traditional Craftsman in the Art of Sekishu Washi Paper, Designated as a Traditional Craft by the Minister of Economy, Trade and Industry
Lives in Misumi-cho, Hamada City, Shimane Prefecture
"Kawahira"
Isao Kawahira
Collaboration of Sekishu Washi Paper and Japanese Umbrellas
Hopes to pass on his skills and share the appeal of his craft through new projects
Q. In April 1989, Sekishu Washi paper was designated as a traditional craft by the Minister of Economy, Trade and Industry. Tell us about the history and characteristics of Sekishu Washi paper.
During the Edo period (1603-1867), paper made in the Iwami region by farmers during the off-season was called Sekishu paper. During the Meiji period (1868-1912), Sekishu Washi paper came to be used as a generic term for paper made in the Iwami region. At its peak, there were more than 6,000 paper-making businesses. Currently, there are four Sekishu Washi Cooperative Association businesses in Misumi-cho, Hamada City.
Sekishu Washi paper has been designated as a traditional craft. There are specific methods for making and drying the paper, and specific materials and tools are used. Craftsmen must pass an inspection by the Sekishu Washi Cooperative Association. One major characteristic is the strength of the paper fibers. Kozo (paper mulberry) is used as a raw material. Its fibers are entangled together to make the paper tough and resistant to tearing when used with its inner bark. Misumi-cho has an environment that allows the cultivation of high-quality kozo, and thanks to the abundance of sources of good water, the entire process from cultivation of raw materials to product processing can be done in an integrated manner. This is a unique feature of the town.
At Kawahira, we use only locally grown kozo. We use traditional methods, resulting in washi paper with a gentle, slightly yellow color.
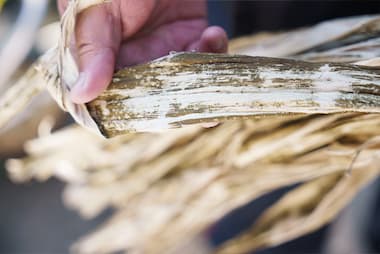
Q. How do you make the Japanese washi paper for Sankaku umbrellas?
The raw material, kozo, is a plant that grows up to three meters each year. It is cut into roughly one-meter pieces and steamed, and then it is peeled and dried so that only the dark-colored bark remains. The process is the same for all washi paper: the outer dark-colored layer is removed, leaving the thin, green-colored inner bark that is boiled and broken up.
There are two ways of making washi paper: tamezuki (to produce thick paper) and nagashizuki (to produce thin paper). The tamezuki method is used to make paper washi for Sankaku umbrellas. Kozo and water are placed in a strainer tank, and an ingredient from the root of the sunset hibiscus (commonly known as neri) is added to thicken the water. Products from overseas and chemical neri are used in some other regions. However, at Kawahira, we use only natural, locally-sourced materials.
Next, scraps of paper from origami cranes that have been unfolded and shredded are added, and then the mixture is strained. The washi paper is then placed on a board and allowed to dry.
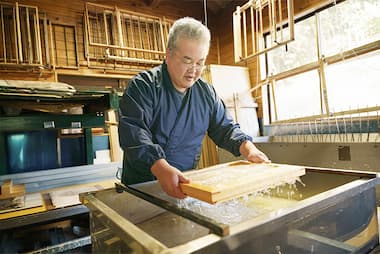
Q. How difficult is it to make washi paper for Sankaku umbrellas?
The difficult part is maintaining the same quality at the desired thickness when adding the scraps of paper. The finished washi paper must be weighed accurately to the nearest 0.1 gram, neither too thick nor too thin. However, the thickness can't be measured during the straining process, because of the water in the mixture. You won't know until the paper is finished. This is where a craftsman shows his skill.
It is also difficult to adjust the amount of neri added. If there is too much neri, the adhesion will be too strong and the water won't drain out sufficiently. However, too little neri will result in an uneven thickness and affect the quality of finished products.
We have just received a request for washi paper made from three different colors of shredded origami paper. Both my father, the second generation, and my grandfather, the founder, made umbrellas from washi paper, so we have the technology for making washi paper for Japanese umbrellas. However, there was some trial and error involved in straining washi paper with the pieces of paper. We started by making smaller sizes of washi paper, like the size of an award certificate, and later expanded to larger sizes.
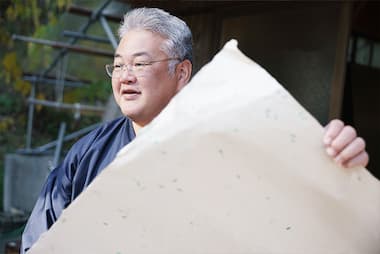
Q. Sankaku umbrellas have attracted a lot of attention, including their unveiling at the G7 Summit.
Rather than deliver the final product, our job is to make the washi paper that is used in the final product. So, we are happy when our materials are used. We are very proud that Sekishu Washi paper was used at the G7 Summit.
We believe it is important for traditional crafts to meet the needs of both sellers and buyers. Creating the materials for Sankaku umbrellas has been a challenging endeavor. I hope that as Sankaku umbrellas become more widely known and seen by many people, it will lead to new sales channels for washi paper.
Q. How do you achieve a balance between tradition and innovation?
Since we do not use chemical neri at Kawahira, our washi paper is both safe and soft. That led us to come up with a product called "first step shoes." The threads and shoelaces are all made of washi paper. We also used Sekishu Washi paper to make autographed uchiwa (paper fans) for the hair-cutting ceremony of former sekiwake-ranked sumo wrestler Okinoumi, who retired in January 2023 and is currently a coach under the name of Kimigahama-oyakata.
My father originally worked in the shipbuilding industry before returning to Misumi-cho. I, too, once worked in another job in Tokyo before returning 15 years ago. So, I believe we both have an outsider's perspective. My father was quick to change from a mortar to a stainless steel strainer tank. He also switched to a titanium board for drying the washi paper. I believe it is necessary to carry on the tradition, but also to be flexible in our thinking to meet the needs of the times.
Q. What are your plans for the future?
We are grateful for collaborations with different industries, such as our recent relationship with Sankaku umbrellas. I am filled with anticipation. I sincerely hope that washi paper will become more widely known from the popularity of Sankaku umbrellas. I look forward to the branches and leaves spreading wide as our industry takes root. First, we must establish a strong record of achievement and actively spread the word.
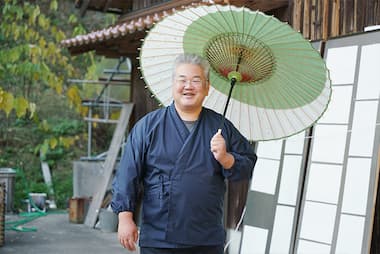